1、 Use Microwave heating technology To dry and sinter to prepare high-purity nano alumina
1. Conventional electric heating equipment takes a long time to dry and sinter, and the heating speed is slow. When heating the furnace cavity, it is easy to pollute the raw materials during heating or high temperature heating, so that the raw materials have low phase and purity is not up to standard; Instead, use microwave drying In high temperature sintering equipment, high-purity aluminum oxide is dried and sintered at a fast temperature rise rate. Microwave drying can be achieved in 20 minutes generally. Heating to an ultra-high temperature above 1450 º C is only 1/5 of the traditional heating time, and continuous production can be achieved. The heating is uniform and pollution-free, realizing high purity of quality.
2. Because microwave heating Due to the characteristics of technology, energy saving, environmental protection and safety can be achieved in the production process.
3. Using microwave drying and high-temperature sintering equipment can shorten the production cycle and reduce the occupation of working capital;
4. At the same time Microwave industrial equipment Easy maintenance, short time, can be stopped and produced according to market demand.
2、 Utilization Microwave high temperature Production of silicon nitride powder and silicon nitride ceramic products by sintering equipment
1. The microwave production of silicon nitride powder adopts the reaction sintering method: the pure silicon powder or the mixture of silicon powder and silicon nitride powder is placed in the Microwave kiln It is filled with nitrogen and nitrided at 1250-1280 ℃ α Silicon nitride powder with hexagonal close packed structure.
2. Sintering of silicon nitride ceramic products: α The mixture of silicon nitride powder is formed according to the general production method of ceramic products, and further nitrided in a microwave kiln filled with nitrogen at 1350~1450 ℃ until all of it becomes β Type silicon nitride with crystalloid structure. The product thus made has stable performance, accurate size, high density and good quality.
3. The traditional hot pressing sintering method is to press and heat sinter silicon nitride powder with a small amount of additives (such as MgO, Al2O3, MgF2, AlF3 or Fe2O3) at a pressure above 19.6MPa and at 1600~1700 ℃. High equipment cost, large land occupation, low output and long production cycle.
4. Advantages of using microwave high-temperature sintering equipment to produce silicon nitride:
① Microwave based heating characteristics and Microwave high-temperature equipment The sintering product has high density and good performance;
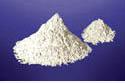
② Energy saving and electricity saving, more than 40% energy saving than conventional electric kiln sintering;
③ The occupied area and investment cost of the equipment are much smaller than those used in the hot pressing sintering method;
④ Different types of silicon nitride products can be produced and sintered in batches, with good production flexibility.
3、 Technical advantages of microwave sintering zirconia and other fine ceramics and electronic ceramics
Zirconia granulating powder is a high-tech biological dental all ceramic material. With the continuous improvement of people's aesthetic requirements, aesthetic and durable dental all ceramic restorations have attracted much attention. The application of all ceramic materials in the past is limited due to the problems of brittleness, beauty and safety. Dental zirconia granulation powder is called ductile ceramics because of its stress-induced phase transformation toughening property. It has high strength and good biocompatibility, and is a new all ceramic material superior to alumina. There are also high-grade household porcelain, high-grade Chinese red porcelain, white porcelain and precision electronic ceramic components, all of which require no deformation, good compactness and no pollution during sintering.
use Microwave equipment The finished products formed by high-temperature sintering have:
1. Overall heating, high compactness, small deformation and high yield of finished products;
2. The heating, heating and heat preservation time is greatly shortened, saving more than 40% of energy;
3. There is no pollution in the product burning process, and the product quality is improved;
4. The equipment is highly automated, easy to control, and saves labor costs;
5. The equipment occupies a small area, and the repair and maintenance time is short, saving the use cost.