1、 At present, microwave sintering equipment is widely used to sinter various high-quality ceramics (such as high-grade household ceramics), fine ceramics, electronic ceramic devices: PZT piezoelectric ceramics, varistors, etc.
The so-called microwave sintering or microwave combustion synthesis refers to the use of microwave radiation to replace the traditional heat source. Uniformly mixed materials or pre pressed billets reach a certain high temperature through their own absorption (or dissipation) of microwave energy, thus triggering combustion synthesis reaction or completing the sintering process. Compared with traditional technology, it belongs to two different heating methods. Therefore, microwave sintering has its own characteristics.
1. Microwave medium heating principle:
Once a chemical material is put into a microwave electric field, the polar and non-polar molecules in it will cause polarization and become even molecules. According to the direction of the electric field, because the electric field belongs to an alternating electric field, the dipole will rotate and vibrate with the change of the electric field, for example, the frequency is 2450MHZ, and the rotation and vibration at 2.45 billion times per second produce an effect similar to the friction between molecules, thereby absorbing the energy of the electric field to generate heat, and the object itself becomes a heating body.
2. microwave heating Difference from traditional heating
When heating in the traditional way, ignition and ignition always start from the surface of the sample, and combustion spreads from the surface to the inside of the sample to finally complete the sintering reaction. When microwave radiation is used, the situation is different. Because of the strong penetration ability of microwave, it can penetrate into the interior of the sample. First, the temperature in the center of the sample rapidly rises to the ignition point and triggers combustion synthesis. The sintering wave propagates radially from inside to outside, which can make the whole sample heated almost uniformly, and finally complete the sintering reaction. The temperature gradient (dT/dt) generated by microwave ignition in the sample is much smaller than that generated by traditional ignition. In other words, the propagation of sintering wave in microwave sintering is much more uniform than that in traditional heating methods.
Experiments show that when the compression density of the sample is high, the propagation rate of the combustion wave caused by the traditional heating method is greatly reduced, and even cannot ignite spontaneously (commonly known as incomplete combustion) due to "self extinction". However, if microwave irradiation is used, as the temperature rise is the result of the absorption (or diffusion) of microwave energy by the reaction material itself, as long as the microwave source continuously gives energy, the sample temperature will soon reach the ignition temperature (T1). Once the reaction is initiated, the heat released will further increase the sample temperature to the combustion temperature (T2), and the sample's ability to absorb microwave radiation will also increase, which ensures that the reaction can be carried out at a sufficiently high temperature (T3>T1) until the reaction is complete.
3. Microwave combustion synthesis or microwave sintering is a controllable process
We can artificially control the propagation of combustion wave by adjusting a series of parameters according to the requirements of product properties. This is a significant advantage of microwave combustion synthesis compared with traditional technology. The microwave power can be adjusted by directly using a microwave source with adjustable power to control the absorption (or dissipation) of microwave energy by the sample. Make the product performance more in line with our requirements.
II Microwave high temperature sintering roller kiln Application in high-grade household porcelain
Through our company and a company in Chaozhou, Guangdong, we used Microwave high temperature Experiment and application of sintering roller kiln (plain firing and glaze firing) Microwave equipment It has the following advantages in high-end household porcelain:
1. The quality of the product has been greatly improved, which is mainly reflected in the enhanced density, vivid and bright color of the product, and no deformation.
2. The firing time of the product is greatly shortened, and the production efficiency is greatly improved.
3. The scrap rate of products is reduced, and the product qualification rate is about 98%.
4. It can achieve computer control and automatic production and reduce labor costs.
5. According to the comprehensive calculation, the energy saving is more than 40% compared with the traditional kiln.
3、 Picture of microwave high-temperature sintering roller kiln and picture of fired products
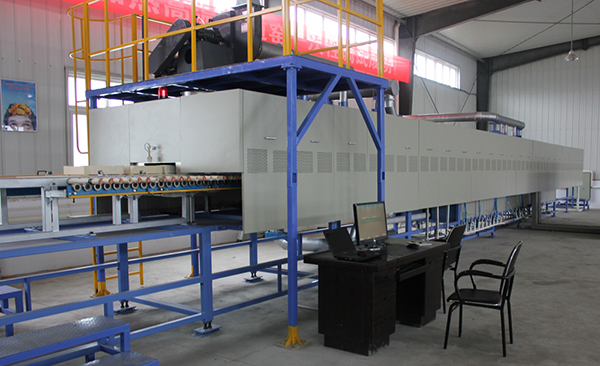
RWEG Microwave high temperature roller kiln (Figure 1)
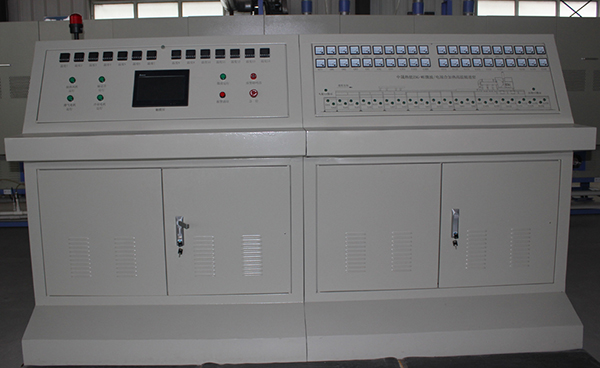
Electric control system of RWEG microwave high-temperature roller kiln (Figure 2)
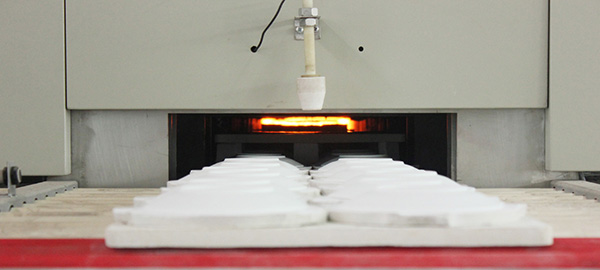
Outlet of RWEG microwave high-temperature roller kiln (Figure 3)
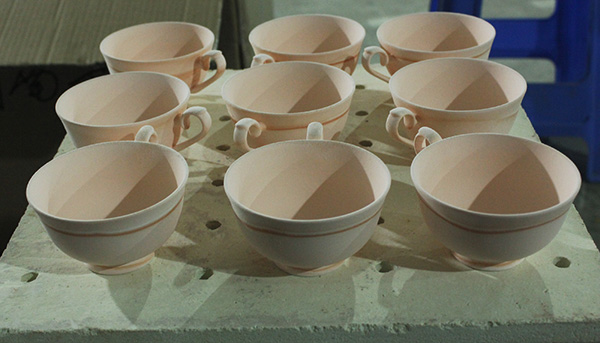
Before sintering of high-grade household porcelain in RWEG microwave high-temperature roller kiln (Fig. 4)
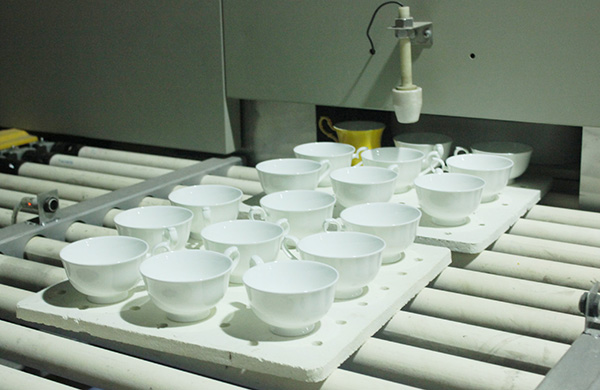
After sintering high-grade household porcelain in RWEG microwave high-temperature roller kiln (Fig. 5)