I microwave heating Principle of energy conservation and efficiency increase in mining industry
1. The energy consumption of minerals in crushing process accounts for 50~70% or more of the energy consumption of the whole process, and the processing of general minerals can meet the requirements by changing the physical characteristics (particle size and concentration of minerals) of minerals. Finding more effective ways to reduce energy consumption in mineral processing and simplifying physical changes in materials can improve the economic benefits of the entire processing.
2. The local heating of mineral particles causes microcracks and brittleness of materials, which will lead to more efficient grinding. The use of microwave heating will enhance this local heating. High energy mineral particles are heated for a long time (calculated in seconds) or increase heat energy to cause phase or chemical changes, thus generating more internal stress and improving the next process. The research shows that microwave radiation is an effective method to improve mineral comminution, because microwave increases the transgranular and intergranular fracture of minerals.
3. The potential advantages of microwave in mining crushing processing to reduce energy consumption are shown in changing the surface chemistry of minerals and promoting the formation of new smelting methods in more controllable environments. If microwave technology can be fully applied, so that every mineral can be processed by microwave, the operation cost of the entire mining industry will be reduced. Adding or directly using microwave in the grinding and conveying process will easily and efficiently reduce the grinding energy cost by 25%.
II Microwave equipment Several Practical Applications of GIS in Mining Processing
1. Drying is the simplest and more economical application of microwave energy. The purpose of drying is to dehydrate, including free water and structural water. Water has the strongest microwave absorption ability, and can completely dry free water and structural water when the temperature is controlled at about 100 ℃~300 ℃. At the same time, some minerals with good wave absorption ability are heated and cracked to improve the subsequent mineral crushing and grinding process.
2. Another application of carbon regeneration microwave heating is the regeneration of activated carbon. Typical carbon regeneration is completed on the conveyor belt of electricity, natural gas or other energy sources. Direct microwave heating reduces energy consumption and carbon loss. When a mild and controllable operating system is used, carbon suddenly changes.
3. Microwave radiation pretreatment of flotation can effectively improve the surface characteristics of ilmenite and improve the flotation capacity of minerals.
For example, ilmenite, the metal oxide of titanium and iron, is 2.45GHz Microwave Oven It has fast dielectric heating characteristics. It is found that under 2600W power radiation, the bulk sample of ilmenite reaches 180 ℃ in 10 seconds and 720 ℃ in 1 minute; Quartz and feldspar have only a small microwave heating performance, and can only reach 53 ℃ and 65 ℃ after 1 minute. After microwave irradiation, the recovery of ilmenite increased by more than 20%. With the microwave radiation, the local surface area of ilmenite samples has changed significantly, and new phases have been observed. When ilmenite (iron titanium, FeTiO3) appears in the air, it will be oxidized, and Fe+2 will be oxidized to Fe+3. At room temperature, this oxidation rate is very slow, but it will accelerate with the increase of temperature. Microwave selective heating characteristics accelerate the oxidation of Fe on the surface of ilmenite, and oxidation enhances the wave absorption performance of flotation reactants, thus improving the flotation speed. The research results show that the recovery of ilmenite under microwave irradiation for 10 seconds increases by 10%, and with the increase of microwave irradiation time, the recovery of ilmenite increases by about 64%, up to 87%. The recovery of minerals is completed by improving the surface chemical properties of flotation minerals. Microwave radiation can reduce the consumption of sodium oleate. When the recovery rate of ilmenite flotation reaches 60%, the consumption of sodium oleate is 2 × 10-4 mol; about Microwave processing Of ilmenite, sodium oleate consumption is 7 × 10-5 mol, the recovery rate reaches 65%.
4. The application of calcination microwave energy also appears in the industrial production of mining industry, especially in refractory minerals and their smelting. For example, the typical refractory arsenic bearing pyrite pyrite gold ore requires calcination, high pressure and filtration to extract gold, and high pressure and calcination finally lead to problems. Using the selective absorption principle of microwave, only part of the ore can work with microwave. In this way, valuable energy can be saved and some by-products can be avoided to stay on the production line.
5. The baking of gold smelting standard is to oxidize the iron and sulfur in pyrite. Considering the economic benefit, the heat released from the oxidation of sulfur in pyrite is used during processing. Microwave equipment can successfully carry out the selective oxidation of iron and separate sulfur well. Pyrite is directly processed into hematite by controlling the temperature below the burning point of sulfur and controlling the oxygen content. We can use microwave technology equipment to complete the oxidation in the liquefaction reaction bed.
6. Hematite calcite is produced by the traditional calcination of arsenic bearing pyrite in gold smelting of arsenic bearing pyrite, and the by-products are SO2 and AsO3. By controlling the reaction conditions and changing the reaction products to form magnetite, AsS and SO2, this reaction can be carried out continuously in the liquefaction bed under the condition of reducing the oxygen content by using microwave to provide reaction conditions.
7. Carbon bearing minerals Organic carbon in carbon bearing minerals is very suitable for microwave processing, and CO2 gas is formed by rapid microwave heating.
8. Chalcopyrite smelting uses the same method as gold smelting to smelt copper by microwave. By effectively controlling the heating rate and oxygen content, acid is generated when the gas escapes. It is proved that microwave processing can effectively oxidize sulfur. The recovery rate of copper dissolved in acid is more than 99%.
9. Microwave treatment of mineral tailings Mineral tailings materials processed by microwave shall include goethite, calcite, quartz and jarosite, which contain gold and silver combined with goethite. Nearly 50% of gold cannot be filtered by CN (cyanide). Microwave pretreatment of tailings and CN filtration of calcite are used to obtain high gold recovery. The by-product of the reaction of crushing goethite is only water.
10. The massive metal sulfide ore has been analyzed and studied for several metal sulfide ores, including Pb and Zn combined with Cu, Au, Co, Ag. Almost all metal sulfides have shown the characteristics of microwave heating. The research confirms that the selective oxidation technology for microwave processing of complex massive sulfide is feasible.
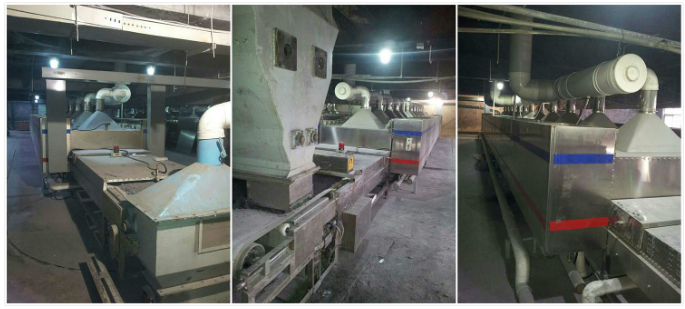