I microwave heating Principle of energy conservation and efficiency increase in mining industry
one In the mineral processing industry, the energy consumed by mineral crushing accounts for fifty ~ seventy %Crushing changes the physical properties of minerals (particle size and concentration of minerals) to improve the economic benefits of the whole process.
two Heating minerals can cause microcracks and brittleness of materials, which will have more efficient crushing and grinding effects. Because mineral heating or increasing heat energy for a long time will cause phase or chemical changes, which will generate more internal stress and improve the crushing and grinding effects. Microwave radiation is an effective method to improve mineral crushing, because it increases the transgranular and intergranular fracture of minerals 。
3、 Microwave can reduce energy consumption in mining crushing processing, which is shown in that microwave can easily and efficiently reduce 25% of the grinding and crushing energy costs.
II Several applications of microwave in mineral processing and mineral processing
one Drying: Drying is the simplest and more economical application of microwave energy. The purpose of drying is to dehydrate, including free water and structural water. Water has the strongest microwave absorption ability, and can completely dry free water and structural water when the temperature is controlled at about 100 ℃~300 ℃. At the same time, some minerals with good wave absorption ability are heated and cracked to improve the subsequent mineral crushing and grinding process.
two Flotation: microwave radiation heating can effectively improve the surface characteristics of ilmenite and improve the flotation capacity of minerals 。
For example, ilmenite, the metal oxide of titanium and iron 2.45GHz Of Microwave Oven It has fast heating characteristics. Research findings 2600W Under power radiation, the mass sample of ilmenite ten Within seconds one hundred and eighty ℃, one Arrive in minutes seven hundred and twenty ℃; Quartz and feldspar have only a small microwave heating performance, corresponding to one Only after minutes fifty-three ℃ and sixty-five ℃。 Ilmenite recovery increases after microwave radiation twenty %Above. With the microwave radiation, the local surface area of ilmenite samples has changed significantly, and new phases have been observed. When ilmenite (iron and titanium, FeTiO3 )Oxidation occurs in the air, Fe+2 Oxidation Fe + three At room temperature, the oxidation rate is very slow, but it accelerates with the increase of temperature. Microwave selective heating accelerates the surface of ilmenite Fe The oxidation of 。
Research results show that microwave radiation ten Increase in recovery of ilmenite ten %With the increase of microwave radiation time, the recovery of ilmenite increases by about sixty-four %, zui is highly accessible eighty-seven %。 Microwave radiation can also reduce the consumption of sodium oleate, and the flotation recovery rate of ilmenite reaches sixty %Amount of sodium oleate two × ten - four mole; about Microwave processing Of ilmenite, sodium oleate consumption is seven × ten - five Mol, recovery rate reaches sixty-five %。
3、 Calcination: Microwave high temperature Application of heating in refractory minerals and their smelting 。
For example, typical refractory arsenic bearing pyrite pyrite gold bearing pyrite requires calcination, high pressure and filtration to extract gold. High pressure and long calcination time consume large energy. Using the selective heating principle of microwave, only part of minerals can work with microwave, which will save energy and avoid the appearance of some refractory by-products and stay on the production line.
four Smelting of gold : Encapsulated gold minerals are processed by traditional methods, and the gold precipitation rate is only 60% For example, if microwave heating is used first, the oxide in the gold coating will be heated first and heat will be released to expand, so that the inclusion will burst. In this way, the subsequent precipitation process can increase the precipitation rate of gold to 90% about.
five Smelting of chalcopyrite: Use the same method for smelting gold Microwave Smelting of Copper 。 By effectively controlling the heating rate and oxygen content, acid is generated when the gas escapes. It is proved that microwave heating process can effectively oxidize sulfur. The recovery rate of copper dissolved in acid exceeds ninety-nine %。
six Carbon bearing minerals: The organics in carbon bearing minerals are very suitable for microwave processing. Microwave heating is fast. Its selective heating characteristics can stimulate the decomposition of organics and generate exothermic reactions, reducing energy consumption.
seven Microwave treatment of mineral tailings : Mineral tailings processed by microwave, including goethite, calcite, quartz and jarosite, containing gold and silver combined with goethite, close to fifty %Your gold can't be used CN (Cyanide) filtration. Microwave Pretreatment of Tailings , and then adopt CN High gold recovery rate can be obtained by filtering calcite.
8、 Microwave treatment of red mud, Phosphogypsum : Microwave calcination of phosphogypsum and red mud CaO-SiO two -Al two O three Recombination to obtain useful sulfuric acid H two SO four , Alumina Al two O three , engineering building materials CaO · SiO two ; To achieve "slag control" and "eat dry and squeeze clean". Microwave heating roasting is adopted to reduce the firing temperature, expand the firing temperature range, improve the clinker quality and kiln production capacity, and the new process will not add a lot of other substances and will not produce new pollution.

3、 Industrial application cases of microwave beneficiation and mineral processing
1. Calcination of mica ore: it can effectively increase the number of layers of mica, and improve the output and quality of pearlescent powder ground in the subsequent process.
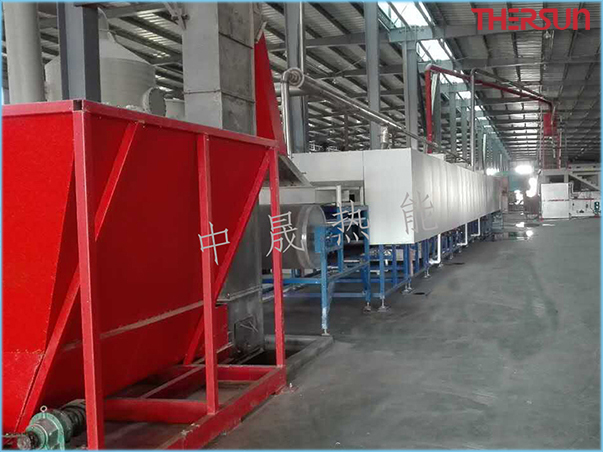
Microwave calcination of mica ore
2. Drying of tungsten ore: high efficiency, large output, improved working environment and reduced external emissions.
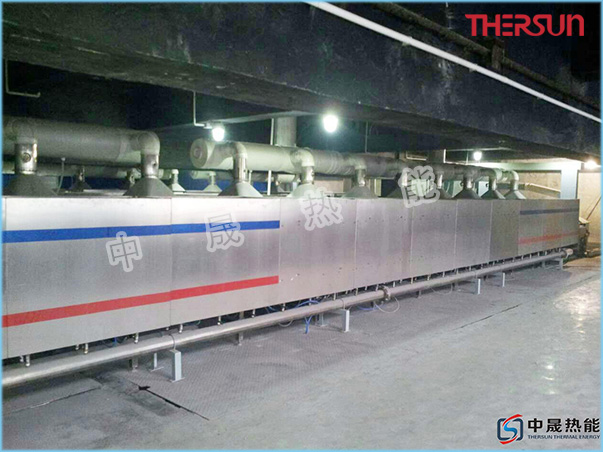
Tungsten ore microwave drying
3. Microwave heating tailings slag to prepare foamed ceramics, traditional electrical heating, foaming time 6 hours, microwave foaming only 2.5 hours, energy saving more than 40%.
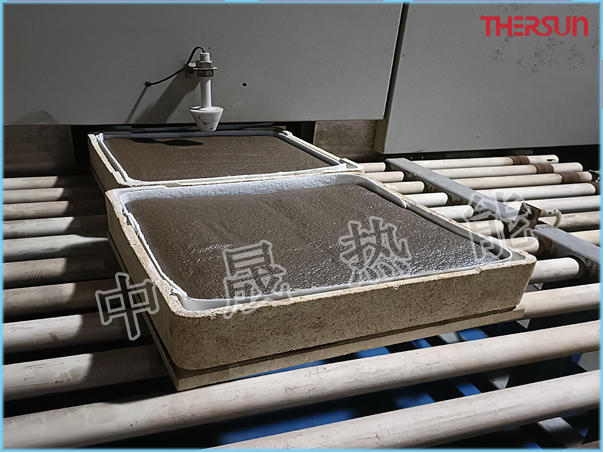
Preparation of Foamed Ceramics by Microwave Heating of Tailings Slag